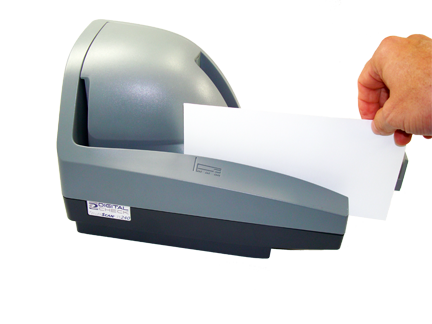
Yet, even as easy as it is, this important detail is often overlooked. While researching our recent white paper about check scanner maintenance, we found that a simple lack of cleaning was by far the leading cause of preventable support calls and repair requests – and half or more of our customers either followed no set schedule for maintenance, or never cleaned their scanners at all.
For those of us who’ve been in the business long enough to remember the large reader/sorter machines of the past, this is a somewhat shocking piece of information – in those days, maintenance was always a formal part of the customer’s processes and budgets, and organizations stuck to meticulous schedules. What changed? Did people just get lazy?
Well, the answer is that check scanner technology has advanced over the past 15 years. Back in 1996 at BAI’s Image Technology in Banking Conference companies like IBM, NCR, and Unisys had reader/sorters that required large booths to display them. These were room-sized pieces of equipment costing upwards of a million dollars, and going months or years without cleaning such a device would have been unthinkable. On top of the purchase price, banks would add an extra 10% for maintenance contracts to have technicians properly clean and maintain the equipment on a monthly basis. For big-ticket electronics on that scale, it was a worthwhile investment of time and money.
Now, of course, things have changed. Check scanners have been reduced from a large-room-sized footprint to the size of an office desktop telephone, or even a coffee mug. Instead of one machine serving an entire bank from a central location, with a dedicated staff of trained operators, the workload is spread across thousands of smaller devices, with a front-line teller, or at best a branch manager, as the person usually responsible for operating and maintaining each one. Although each scanner is much smaller in size, though, their overall mission-critical nature has not changed. An organization cannot afford to have scanners out of commission or performing poorly due to lack of maintenance. Moreover, now that the process of scanning checks has moved from the back office out to the teller window, poorly functioning equipment is something that can affect the customer’s experience, not just that of your operations staff. And – a bit ironically – because the cleaning process itself has become so easy, that’s made a lot of people think it’s not very important.
Digital Check recommends that organizations establish a plan for both routine operator maintenance and for preventative maintenance and scanner repair. Whether it means cleaning your equipment weekly or monthly, having a plan will save time and money. Even when you factor in the price of cleaning cards and other supplies, the cost of preventative maintenance is several times less than that of repeated false-alarm support and service calls, or of image-quality errors in your processing queue.
Business-critical applications such as teller or branch capture can benefit from a local swap pool so that a scanner can be replaced within minutes, and disruption to service is minimized. A rule of thumb is to have a swap pool with 10% of your organization’s overall install base of scanners in order to quickly swap out devices requiring maintenance or repair (this also gives you a ready supply of equipment for expansions and upgrades).
Even though the size of the scanner has been reduced, the need for proper maintenance and cleaning hasn’t gone away – it’s just different. For a handy list of training materials, video tutorials, and to order supplies directly, visit www.digitalcheck.com/clean (our white paper on cleaning and maintenance can also be found here). For more information on Digital Check’s maintenance and repair programs, or about our “train-the-trainer” programs for banks and companies with large numbers of scanners deployed, contact us at 847-446-2285 or fill out our web contact form.